Development of the Company’s corporate information systems
In the reporting year, the Company continued to develop corporate information systems. In 2025, the Company plans to continue developing its corporate information systems.
Sl.No. | Corporate information systems | Development activities |
---|---|---|
1. | Automated information system for processing customer calls | Some features were taken from the corporate software package (CSP) and integrated into a local platform for automated registration, handling of requests, processing of calls, and generation of statistical reports. AIS for processing customer calls was put into operation and included in the Register of domestic software. The Company acquired intellectual property rights to the AIS for processing customer calls |
2. | Corporate software package (CSP) |
|
3. | Electronic document management system (EDMS) |
|
4. | Automated equipment repair control system (AERCS) |
|
5. | Production asset management system (PAMS) | The Repair Schedules subsystem was implemented to automate the scheduling of equipment repairs by integrating the PAMS and AERCS software packages. |
6. | Corporate information system ‘1C:Enterprise. Management of a manufacturing organisation’ |
|
7. | Automated information system for payroll calculation and personnel management (PPM) |
|
8. | System for electricity transport metering |
|
9. | Automated system for calculation of labour costs for modifications (AS CLCM) | The AS CLCM was put into operation. It is designed to calculate labour costs and account for services under contracts for the maintenance of the Company’s corporate information systems. |
10. | Unified integration platform (UIP) | As part of the trial operation of the UIP, work continued to refine the interaction with customers of Rosseti Group in terms of business processes for providing services and interacting with customers |
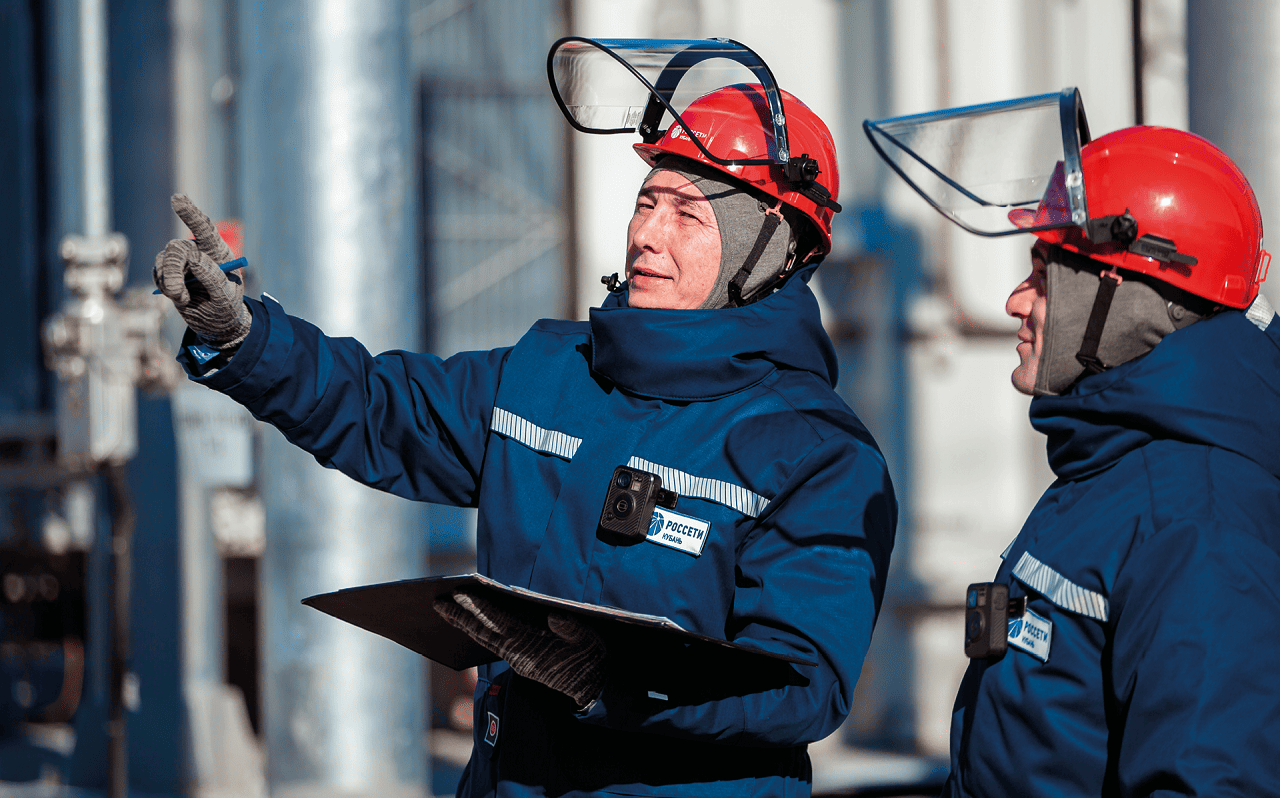